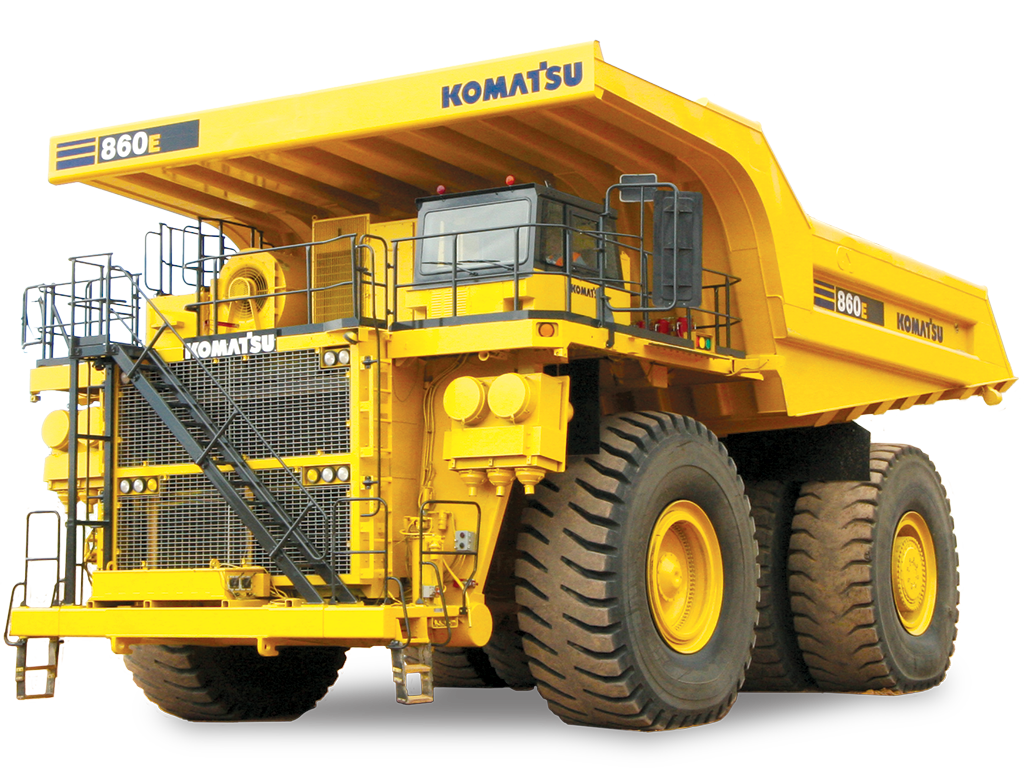
Komatsu 860E-1K ELECTRIC TRUCKS
Product Feature
4650 Horsepower Continuous Retarding Capability
The 3469 kW 4,650 HP retarding system provides state of-the-art braking capacity for navigating today’s mining applications which contain steep continuous descents and sharp switchbacks.
Castings Used in High Stress Areas
To increase frame reliability, steel castings have been incorporated at key frame pivot points and key load bearing critical portions of the frame. This includes the rear body pivot and horsecollar sections.
Dynamic Retarding
For daily operation, the 860E-1K is equipped with an electric retarding package which can supply up to 3469 kW 4,650 hp of resistance. When requested, the wheel motors switch from motors to electrical generators. The resistive force created from this process is used to slow the truck to the desired speed. The power generated is then run over an 18 element grid which converts the electricity into heat. The heat is then dissipated into the atmosphere by the quietest grid blower Komatsu has ever used.
Ergonomically Designed Cab
The Komatsu 860E-1K cab design provides the operator with an environment where they can be comfortable and confident during operation. The rubber mounted isolated cab includes tinted safety glass, power windows, heating and air conditioning, acoustical insulation, double sealed doors, and filtered, pressurized air.
Fully Hydraulic Controlled Multiple-Disc Wet Brakes
The 860E-1K comes standard with four-wheel, hydraulically actuated, oil cooled service brakes. In the event that the truck’s hydraulic system pressure drops below an acceptable level, accumulator tanks will automatically apply all wheel brakes to bring the truck to a complete stop.
Hill Start
With the new Komatsu Drive System comes a new innovation in electric truck technology. The Hill Start feature allows the operator to start the machine on a grade without roll back.
Hydropneumatic Suspensions
Hydrair® II suspension cylinders located at each wheel provide a smooth and comfortable ride for the operator and dampen shock loads to the chassis during loading and operation.
Komatsu AC Electric Drive System
The Komatsu drive system, utilizing Siemens AC control, offers independent control of the rear wheelmotors. This provides outstanding traction during wet and slippery conditions, thus improving tire wear and operator confidence.
Payload Policy
Recognizing that variation occurs naturally in material density, fill factors, and loading equipment, Komatsu America Corp. deems it necessary to establish a consistent loading policy for the 860E-1K. This loading policy is intended to identify the guidelines for the loading of Komatsu Mining Trucks, and is valid for approved applications and haul profiles only (see chart below).
Steering
By using double acting hydraulic steering cylinders with a six-point articulation linkage, the 860E-1K power steering system provides positive steering control with minimal operator effort. The turning circle has a diameter of 31 m 102 ft. The accumulator-assist steering system surpasses requirements set forth by ISO 5010.
Traction Control
During slippery conditions caused by inclement weather and/or application severity, the 860E-1K traction control technology utilizes information from all four wheels to detect and correct wheel spin and/or slide events. Traction Control operates automatically and independently of the service brakes, providing a more efficient means of controlling the machine in inclement conditions.
Trolley (optional)
The factory installed 860E-1KT trolley system allows for faster ascent up grades, providing higher production and lower fuel consumption compared to conventional diesel systems.
Body
All-welded steel flat floor body with horizontal bolsters and full canopy. Tapered body, body up sling and frame mounted rubber pads are standard. Heated body optional.
Braking System
Max. service apply pressure | 2,400 psi | 16547 kPa |
Total friction area per brake | 11,693 in² | 75439 cm² |
Secondary brakes | Automatically applied prior to hydraulic system pressure dropping below level required to meet secondary stopping requirements. | |
Wheel brake locks | Switch activated | |
Parking brakes | Multiple disc, spring-applied, hydraulically-released, dry brakes on inboard end of each wheel motor rotor shaft. Rated to hold on ±15% grade at maximum gross vehicle weight. | |
Electric dynamic retarder | 4,650 hp | 3469 kW |
Continuously rated high-density blown grids w/retard capacity at low speeds and retard in reverse propulsion. |
Cab
Advanced Operator Environment with isolation mounted, integral 4- post ROPS/FOPS Level 2 structure. Adjustable air suspension seat w/lumbar support, arm rests, and 3-point seat belt, full-size passenger seat, thermal insulation, tilt and telescoping steering wheel, electric windshield wipers w/washer, tinted safety glass, power windows, Komatsu Payload Weighing System, 61,000 Btu/hr heater and defroster, 19,900 Btu/hr air conditioning (HFC - 134A refrigerant).
Cooling System
L&M radiator assembly, split-flow, with deaerator-type top tank.
Electric Drive
AC/DC CURRENT | ||
Drive System* | Komatsu AC Drive | |
Alternator | DRLDZ5010-AL | |
Dual Fan Main Blower | 14,800 cfm | 419 m³/min |
Control | IGBT AC Torque Control System | |
Ratio | 35.52:1 | |
Speed (maximum) | 40 mph | 64.5 km/h |
* Wheel motor drive system application depends upon gross vehicle weight, haul road grade, haul road length, rolling resistance and other parameters. Komatsu must analyze each job condition to assure proper application. |
Electric System
Alternator | 24 volt, 140 amp | |
Lighting | 24 volt | |
Cranking motors | Two/24 volt |
Engine
Make and model | Komatsu SSDA16V160 Tier 2 | |
Fuel | Diesel | |
Number of cylinders | 16 | |
Operating cycle | 4 cycle | |
Gross horsepower* @ 1900 rpm | 2,700 HP | 2014 kW |
Net flywheel power** @ 1900 rpm | 2,550 HP | 1902 kW |
Weight (wet) | 21,182 lb | 9608 kg |
* Gross horsepower is the output of the engine as installed in this machine, at governed rpm and with engine manufacturer’s approved fuel setting. Accessory losses included are water pump, fuel pump and oil pump. | ||
**Net flywheel power is the rated power at the engine flywheel minus the average accessory losses. Accessories include fan and charging alternator. Rating(s) represent net engine performance in accordance with SAE J1349 conditions. |
Frame
Plate material tensile strength steel |
70,000 psi | 482.6 mPa |
Casting material tensile strength steel |
90,000 psi | 620.5 mPa |
Rail width | 12'' | 305 mm |
Rail depth (minimum) | 34'' | 864 mm |
Top and bottom plate thickness | 1.57'' | 40 mm |
Side plate thickness / Rear | 0.75'' | 19 mm |
Side plate thickness / Front | 0.87'' | 22 mm |
Drive axle mounting | Pin and spherical bushing | |
Drive axle alignment | Swing link between frame and axle |
Hydraulic System
Steering | Accumulator assisted with twin double acting cylinders provide constant rate steering. Secondary steering automatically supplied by accumulator. | |
Turning circle diameter (SAE) | 102' | 31 m |
Reservoir | 250 U.S. gal | 947 L |
Filtration | In-line replaceable elements | |
Suction | Single, full flow, 100 mesh | |
Hoist and steering | Dual, in-line, high pressure | |
Brake component cabinet | Above deck, easily accessible with diagnostic test connections | |
Hoist | Two 3-stage dual-acting outboard cylinders, internal cushion valve, over-center dampening | |
Hoist times: | ||
Power-up loaded | 22 sec | |
Power-down (high idle) | 13 sec | |
Float-down (low idle) | 23 sec | |
Pumps | Two pumps, single package, end of alternator | |
Hoist and brake cooling | Tandem gear pump with output of 931 lpm / 246 gpm at 1900 rpm and 17237 kPa / 2,500 psi | |
Steering and brake | Pressure-compensating piston pump with output of 246 lpm / 65 gpm at 1900 rpm and 18960 kPa / 2,750 psi | |
System relief pressures: | ||
Hoist and brake cooling | 2,500 psi | 17237 kPa |
Steering and brake | 3,000 psi | 20685 kPa |
Quick disconnects standard for powering disabled truck and for systems diagnostics. |
Service Capacities
Cooling System | 125 U.S. gal | 473 L |
Crankcase | 74 U.S. gal | 280 L |
Hydraulic system | 350 U.S. gal | 1325 L |
Motor gear box (each) | 32 U.S. gal | 121 L |
Inverter cooling system | 6.5 U.S. gal | 25 L |
Fuel | 1,200 U.S. gal | 4542 L |
Reserve Oil® System | 30 U.S. gal | 114 L |
Suspension
Variable rate hydro-pneumatic with integral rebound control
Product Parameter
Floor sheet 200,000 psi / 1379 mPa tensile strength steel / Outer |
0.63'' | 16 mm |
Floor sheet 200,000 psi / 1379 mPa tensile strength steel / Center |
0.75'' | 19 mm |
Front sheet 200,000 psi / 1379 mPa tensile strength steel / Outer |
0.39' | 10 mm |
Front sheet 200,000 psi / 1379 mPa tensile strength steel / Center |
0.39' | 10 mm |
Side sheet 200,000 psi / 1379 mPa tensile strength steel |
0.31'' | 8 mm |
Canopy sheet 100,000 psi / 690 mPa tensile strength steel |
0.24'' | 6 mm |
Capacity struck | 160 yd³ | 122 m³ |
SAE heaped 2:1 | 221 yd³ | 169 m³ |
Standard Komatsu body weight | 74,171 lb | 33643 kg |
Max. service apply pressure | 2,400 psi | 16547 kPa |
Total friction area per brake | 11,693 in² | 75439 cm² |
Secondary brakes | Automatically applied prior to hydraulic system pressure dropping below level required to meet secondary stopping requirements. | |
Wheel brake locks | Switch activated | |
Parking brakes | Multiple disc, spring-applied, hydraulically-released, dry brakes on inboard end of each wheel motor rotor shaft. Rated to hold on ±15% grade at maximum gross vehicle weight. | |
Electric dynamic retarder | 4,650 hp | 3469 kW |
Continuously rated high-density blown grids w/retard capacity at low speeds and retard in reverse propulsion. |
Radiator frontal area | 62.5 ft² | 5.81 m² |
AC/DC CURRENT | ||
Drive System* | Komatsu AC Drive | |
Alternator | DRLDZ5010-AL | |
Dual Fan Main Blower | 14,800 cfm | 419 m³/min |
Control | IGBT AC Torque Control System | |
Ratio | 35.52:1 | |
Speed (maximum) | 40 mph | 64.5 km/h |
* Wheel motor drive system application depends upon gross vehicle weight, haul road grade, haul road length, rolling resistance and other parameters. Komatsu must analyze each job condition to assure proper application. |
Alternator | 24 volt, 140 amp | |
Lighting | 24 volt | |
Cranking motors | Two/24 volt |
Make and model | Komatsu SSDA16V160 Tier 2 | |
Fuel | Diesel | |
Number of cylinders | 16 | |
Operating cycle | 4 cycle | |
Gross horsepower* @ 1900 rpm | 2,700 HP | 2014 kW |
Net flywheel power** @ 1900 rpm | 2,550 HP | 1902 kW |
Weight (wet) | 21,182 lb | 9608 kg |
* Gross horsepower is the output of the engine as installed in this machine, at governed rpm and with engine manufacturer’s approved fuel setting. Accessory losses included are water pump, fuel pump and oil pump. | ||
**Net flywheel power is the rated power at the engine flywheel minus the average accessory losses. Accessories include fan and charging alternator. Rating(s) represent net engine performance in accordance with SAE J1349 conditions. |
Plate material tensile strength steel |
70,000 psi | 482.6 mPa |
Casting material tensile strength steel |
90,000 psi | 620.5 mPa |
Rail width | 12'' | 305 mm |
Rail depth (minimum) | 34'' | 864 mm |
Top and bottom plate thickness | 1.57'' | 40 mm |
Side plate thickness / Rear | 0.75'' | 19 mm |
Side plate thickness / Front | 0.87'' | 22 mm |
Drive axle mounting | Pin and spherical bushing | |
Drive axle alignment | Swing link between frame and axle |
Steering | Accumulator assisted with twin double acting cylinders provide constant rate steering. Secondary steering automatically supplied by accumulator. | |
Turning circle diameter (SAE) | 102' | 31 m |
Reservoir | 250 U.S. gal | 947 L |
Filtration | In-line replaceable elements | |
Suction | Single, full flow, 100 mesh | |
Hoist and steering | Dual, in-line, high pressure | |
Brake component cabinet | Above deck, easily accessible with diagnostic test connections | |
Hoist | Two 3-stage dual-acting outboard cylinders, internal cushion valve, over-center dampening | |
Hoist times: | ||
Power-up loaded | 22 sec | |
Power-down (high idle) | 13 sec | |
Float-down (low idle) | 23 sec | |
Pumps | Two pumps, single package, end of alternator | |
Hoist and brake cooling | Tandem gear pump with output of 931 lpm / 246 gpm at 1900 rpm and 17237 kPa / 2,500 psi | |
Steering and brake | Pressure-compensating piston pump with output of 246 lpm / 65 gpm at 1900 rpm and 18960 kPa / 2,750 psi | |
System relief pressures: | ||
Hoist and brake cooling | 2,500 psi | 17237 kPa |
Steering and brake | 3,000 psi | 20685 kPa |
Quick disconnects standard for powering disabled truck and for systems diagnostics. |
Cooling System | 125 U.S. gal | 473 L |
Crankcase | 74 U.S. gal | 280 L |
Hydraulic system | 350 U.S. gal | 1325 L |
Motor gear box (each) | 32 U.S. gal | 121 L |
Inverter cooling system | 6.5 U.S. gal | 25 L |
Fuel | 1,200 U.S. gal | 4542 L |
Reserve Oil® System | 30 U.S. gal | 114 L |
Max. front stroke | 12.32'' | 313 mm |
Max. rear stroke | 11.50'' | 292 mm |
Max. rear axle oscillation | ±10.4° |
Rock service, tubeless, radial tires: | ||
Standard tire* | 50/80 R57 | |
Optional tire* | 50/90 R57 | |
Flange mount rim | 34'' x 57'' x 6'' rim assembly | 864 mm x 1448 mm x 152 mm rim assembly |
Typical total tire weight | 50,780 lb | 23033 kg |
* Tires should meet application requirements for tkph/tmph, tread, compound, inflation pressure, ply rating or equivalent, etc. |