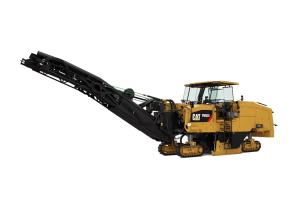
Product Feature
● Efficient performance
Cat® CThe 18 twin turbocharged engine is powerful.,Meet regional emission standards
Auto idle control for smooth operation、Efficient operation,Multiple rotor speeds optimize engine output and power demand
The high-capacity cooling system ensures that the engine is kept at the desired temperature,Thereby improving fuel efficiency.,Reduce emissions
The automatic load sensing function of the rotor adjusts the milling speed,Avoid stall and increase production
● The handling is superb
Reliable and durable track undercarriage,Adopt the time-tested Cat Bulldozer design and automatic tensioning system,And that performance is stable,Longer service life
Robust propulsion system with two independent propulsion pumps,Drive both tracks separately in a high traction cross drive model
Automatic traction control maintains constant speed in the most challenging applications
Four steering modes with advanced calibration and tracking,Provides precise steering geometry,And reduce track pad wear
During operation,Electronically switchable between various rotor speeds
● Comfortable working environment
Height of console is adjustable,The controls are intuitive, easy to use and ergonomically designed,Create a comfortable operation experience for you
When approaching an obstacle,Retractable armrest retracts and redeploys easily
Backlit keyboard,Can work day and night,And employ a wide dispersion and perimeter, LED Lighting options illuminate the work area around the machine
The console is newly upgraded,With optional repositionable suspension seat,Better visibility and comfort
Via the optional remote camera,Cutting edge and conveyor conditions are more visible
Single column、Fold-forward power top option,Comes with overhead LED Lighting and integrated side extension,Can be quickly reclaimed and redeployed during operation,Overhead obstructions can be cleared with the push of a button,An optional windscreen can be added for added comfort
The optional dust extraction system provides maximum dust removal from the work area
● Material unloading
High capacity belt with excellent discharge control,Milling material can be effectively unloaded
Seamless drive belt with wide opening for efficient rotor chamber cleaning
Adjust the belt speed to match the material type and production rate,And the built-in“Pressurization”Function to temporarily increase the speed of the drive belt,To be faster、Eject the item further
Reverse rotation of the drive belt for faster cleaning,While the magnetic vinyl cover quickly checks the rollers for wear
● Improve accuracy with integrated technology
Adopt the belt Grade and Slope Integration of the system Cat GRADE,Automatic and precise repeated cutting can be realized
When repositioning the control box,No need to reconfigure settings,When the work lights are activated,The background color will change to Night Mode
Omnidirectional control from any control box Grade and Slope System
Seamlessly switch between multiple grade sensors,Ensure continuous and precise milling
Adjust the speed when the rotor is cut down,Optimum control of the machine
Set and switch cut-in automatically/Cut-out status,Also save the settings for later up
Use the barrier crossing function,Easily avoid obstacles in the cutting path
Improved for comprehensiveness 3D Milling operation(Requires additional hardware)
● Easy to maintain
Large service door and power hood for easy walk-in access to important components,Make maintenance easier and faster
Maintenance-free track components and easy-to-replace track pads help reduce repair costs
Standard ground control and optional electrically operated rotor rotation with suspension simplify head removal and replacement
High and low pressure flush options allow easy connection to the on-board water tank,And is convenient to clean and maintain
During maintenance,The auxiliary drive system can be used to control some machine functions.
Electrical system wiring is color-coded and digitally identified,Easy to identify,And that surface is cover with a protective wear-resistant nylon braided lay.,Longer service life
Longer hydraulic oil change interval:3000 hours(Oil-free sampling),6000 hours(Oil-containing fluid sampling)
Make use of Cat Product Link™ Telecommunication services,Track scheduled maintenance
Electronic Control Module(ECM,Electronic Control Module)May monitor machine systems and alert the operator of performance issues,Match Product Link When the option,Available locally Cat Dealer offers additional remote services
Multi-piece sleeve type engine filter green environmental protection,It can effectively reduce waste,And that replacement cost is reduce
Convenient parts availability and dealer location,Service kits can be easily ordered for high wear parts
● System K Rotor
Cat System K Rotors feature excellent cutting patterns for a wide range of applications,Fficient and smooth material flow
Dual retention taper design eliminates the need for retention pin、Bolts or screws hold the shoe in place,Speeds replacement and requires no fastener or torque adjustment。
Reversible blades and high strength alloys reduce wear,And that service life of the rotor is prolon
Compare with traditional carbide tool bit,Optional diamond tip extends replacement cycle time by up to 80 times
● Durable cutting system
Heavy-duty dry clutch is adopted for rotor transmission system.、Automatic belt tensioner to prevent slippage and two high tension drive rotors(Five tendons)Drive belt
The cutting chamber is reinforced,More durable
The maintenance has been improved,Implify rotor replacement proces
Hardened full length side slide、Inboard skateboard track shoes and anti-fracture track shoes reduce wear,Reduce the number of maintenance
● Convenience function
Cat Cold planers offer a variety of features and options,Make daily operations and maintenance tasks easier。
During truck replacement,Press the button to pause and resume machine function
Optional magnetic paint can holder
Water hose storage hook
Angle water injection joint
Easily accessible shovel frame
Top and side view of rotor depth indicator
Compressed air connection in the central operator console
Product Parameter
Cutting system |
|
Milling width |
2010 mm |
Maximum milling depth |
330 mm |
Rotor speed |
100/109/118 rpm |
Number of planing tool bits |
178 |
Power train |
|
Rated power |
470 kW |
Engine |
Cat C18 |
Maximum travel speed |
5.9 km/h |
Maximum milling speed |
100 m/min |
Weight |
|
Operating weight |
33330 kg |
Shipping weight |
29430 kg |
Size |
|
Working length - The conveyor belt unfolds |
14.52 m |
Working width |
3.11 m |
Ceiling height |
4.05 m |
Maximum filling height |
4.86 m |
Minimum Right Cutting Radius |
2 m |
Minimum Left Cutting Radius |
2 m |
Swing angle of conveyor belt |
60 degrees off center |
Transport length |
12.43 m |
Transport width |
2.48 m |
Transport height |
3 m |
Maintenance refill capacity |
|
Cooling system |
85 l |
Engine oil |
65 l |
Fuel tank |
1108 l |
Diesel engine tail gas treatment fluid(DEF)Box |
47 l |
Water spray system tank |
3400 l |
Hydraulic oil tank |
113 l |